Table of contents
Axial deep groove ball bearings
- Bearing design
- Load carrying capacity
- Compensation of angular misalignments
- Lubrication
- Sealing
- Speeds
- Noise
- Temperature range
- Cages
- Internal clearance
- Dimensions, tolerances
- Suffixes
- Structure of bearing designation
- Dimensioning
- Minimum load
- Design of bearing arrangements
- Mounting and dismounting
- Legal notice regarding data freshness
- Further information
Axial deep groove ball bearings
Axial deep groove ball bearings:
- are standardised, ready-to-fit units with high axial load carrying capacity ➤ Figure and ➤ Figure
- are suitable exclusively for the support of predominantly axial loads ➤ section
- are particularly suitable where the bearing position is subjected to high axial loads from one or both sides, but the requirements for axial load carrying capacity are not so high that axial cylindrical roller bearings with even higher load carrying capacity must be used
- permit higher speeds than roller or needle roller and cage assemblies ➤ Figure
- compensate, in conjunction with a spherical housing locating washer, static misalignments between the shaft and housing ➤ section
Axial deep groove ball bearing: nG = limiting speed Fa = axial load Ca = basic axial dynamic load rating |
![]() |
Bearing design
Design variants
Axial deep groove ball bearings are available as:
Basic bearing design
Non-self-retaining, easy-to-fit bearing units
Axial deep groove ball bearings are part of the group of axial ball bearings. The bearings are of a multi-piece construction and, due to their design, are not self-retaining. As a result, it is possible to mount the bearing parts (shaft locating washer, housing locating washer, ball and cage assembly, support washer) separately from each other. In order to guide the balls, the shaft and housing locating washer have raceway grooves (formed rolling element raceways) with a defined osculation, in which the rolling elements circulate. The ball set is retained by a sheet steel cage or a solid brass cage ➤ Table. When using these bearings, the designer does not need to produce the bearing parts for his bearing arrangement and match these to each other himself, but can instead use a standarised, ready-to-fit unit.
Single direction axial deep groove ball bearings
Ready-to-fit bearing unit for compact axial designs
These axial deep groove ball bearings comprise a shaft locating washer, a housing locating washer and a ball and cage assembly ➤ Figure. In order to ensure centring of the washers with a precise fit, the bore of the shaft locating washer (d) is ground. In contrast, the bore of the housing locating washer (D1) is more generously dimensioned and is turned. The housing locating washer can be flat or spherical and can be configured with or without a support washer. The support washers U2 and U3 must be ordered in addition to the bearing.Load carrying capacity of single direction bearings ➤ section.
Axial deep groove ball bearings, single direction Fa = axial load
|
![]() |
Double direction axial deep groove ball bearings
Ready-to-fit bearing unit, suitable for combination with support washers
Double direction bearings comprise a shaft locating washer, two housing locating washers and two ball and cage assemblies ➤ Figure. They can also be combined with support washers U2 and U3. The housing locating washers and ball sets correspond to the designs of the single direction bearings. Load carrying capacity of double direction bearings ➤ section.
Axial deep groove ball bearings, double direction Fa = axial load
|
![]() |
Load carrying capacity
Axial deep groove ball bearings are suitable for the support of predominantly axial loads. They must not be subjected to predominantly radial loads.
Single direction bearings
Single direction axial deep groove ball bearings can support axial forces in one direction and support the shaft on one side ➤ Figure.
Double direction bearings
Double direction axial deep groove ball bearings support axial forces in both directions and can guide the shaft on both sides ➤ Figure.
Compensation of angular misalignments
Axial deep groove ball bearings react with high sensitivity to angular misalignments. In cases where the contact face for the housing locating washer is not vertical (perpendicular) to the bearing axis, the angular misalignment can be compensated by means of bearings with a spherical housing locating washer and support washer ➤ Figure.
Single direction bearings
Series 511, 512, 513, 514 do not permit angular adjustment
Bearings of series 511, 512, 513 and 514 have a flat housing locating washer. As a result, they do not permit angular misalignment or skewing between the shaft and housing.
Series 532, 533 permit angular adjustment
Bearings of series 532 and 533 have a spherical housing locating washer. With an appropriate housing design and in conjunction with support washers U2 and U3, they are variable in angle as a result and can therefore tolerate static misalignments of the shaft relative to the housing within certain limits.
Double direction bearings
Series 522, 523 do not permit angular adjustment
Bearings of series 522 and 523 have two flat housing locating washers and do not permit angular adjustment.
Series 542, 543 permit angular adjustment
Bearings of series 542 and 543 have spherical housing locating washers. With an appropriate housing design and in conjunction with support washers U2 and U3, they are variable in angle as a result and can therefore tolerate static misalignments of the shaft relative to the housing within certain limits.
Lubrication
Oil or grease lubrication is possible
The bearings are not greased. In order to prevent direct metallic contact between rolling elements, raceways and cages, they must be lubricated. Oil or grease lubrication is suitable. The lubricant reduces the wear and also protects the surfaces against corrosion. The choice of lubricant is essentially dependent on the operating temperatures and the speeds; it is also influenced, however, by the load, mounting position, osculations etc.
If there is any uncertainty regarding the suitability of the selected lubricant for the application, please consult Schaeffler or the lubricant manufacturer.
Sealing
The bearings are of an open design
Axial deep groove ball bearings are supplied without seals. As a result, sealing of the bearing position must be carried out in the adjacent construction. This must reliably prevent:
- moisture and contaminants from entering the bearing
- the egress of lubricant from the bearing
Speeds
Limiting speeds and reference speeds in the product tables
Two speeds are generally indicated in the product tables:
- the kinematic limiting speed nG
- the thermal speed rating nϑr
Limiting speed
The limiting speed nG is the kinematically permissible speed of a bearing. Even under favourable mounting and operating conditions, this value should not be exceeded without prior consultation with Schaeffler ➤ link. The values in the product tables are valid for oil lubrication.
Values for grease lubrication
For grease lubrication, 75% of the value stated in the product tables is permissible in each case.
Reference speeds
nϑr is used to calculate nϑ
The thermal speed rating nϑr is not an application-oriented speed limit, but is a calculated ancillary value for determining the thermally safe operating speed nϑ ➤ link.
Noise
Schaeffler Noise Index
The Schaeffler Noise Index (SGI) is not yet available for this bearing type ➤ link. The data for these bearing series will be introduced and updated in stages.
Temperature range
Limiting values
The operating temperature of the bearings is limited by:
- the dimensional stability of the bearing washers and rolling elements
- the support washers
- the cage
- the lubricant
– 30 °C to +150 °C
Possible operating temperatures for axial deep groove ball bearings ➤ Table. The support washers are made from rolling bearing steel and are suitable for the same temperatures as the bearing washers and rolling elements. The temperature limit values of the lubricant must be observed.
Permissible temperature ranges
Operating temperature |
Axial deep groove ball bearings |
---|---|
|
–30 °C to +150 °C |
In the event of anticipated temperatures which lie outside the stated values, please contact Schaeffler.
Cages
Sheet steel cages or solid brass cages are used as standard
Standard cages for axial deep groove ball bearings ➤ Table. Other cage designs are available by agreement. With such cages, however, suitability for high speeds and temperatures as well as the basic load ratings may differ from the values for the bearings with standard cages. Bearings with sheet steel cages do not have a cage suffix ➤ Table.
If there is any uncertainty regarding cage suitability for a specific application, please consult Schaeffler.
Cage, cage suffix, bore code
Bearing series |
Sheet steel cage |
Solid brass cage |
---|---|---|
MP | ||
Bore Code | ||
511 |
up to 28 |
from 30 |
512 |
up to 28 |
from 30 |
513 |
up to 20 |
from 22 |
514 |
up to 11 |
from 12 |
522 |
up to 28 |
from 30 |
523 |
up to 20 |
from 22 |
524 |
06 to 11 |
‒ |
532 |
up to 28 |
from 30 |
533 |
up to 20 |
from 22 |
534 |
06 to 11 |
‒ |
542 |
up to 28 |
from 30 |
543 |
up to 20 |
22, 24 |
544 |
06 to 11 |
‒ |
Internal clearance
Axial clearance and preload is determined by the application
In the case of axial deep groove ball bearings, the internal clearance (axial clearance) is only achieved when the bearings are mounted. The requisite axial clearance of the bearing arrangement is dependent on the application and must take account of the conditions in the bearing arrangement while warm from operation and subjected to load. If axial deep groove ball bearings are subjected to vibrations while under predominantly static load, they must be lightly preloaded. Preload can be applied, for example, using housing nuts ➤ Figure. Other suitable means include shaft nuts, disc springs, calibrated plates (shims) etc. It must always be ensured that no slippage occurs in operation between the rolling elements and raceways ➤ section. It must also be ensured that the preload does not exceed the optimum value, otherwise there will be an increase in friction and therefore in heat generation in the bearing. These will both have a negative effect on the operating life of the bearings.
If there is any uncertainty regarding the setting of the axial clearance, Schaeffler must always be consulted.
Setting the axial clearance of a double direction axial deep groove ball bearing by means of a housing nut
|
![]() |
Dimensions, tolerances
Dimension standards
Bearings with a flat locating surface on the housing locating washer correspond to ISO 104:2015 or DIN 616:2000 and DIN 711:2010 as well as DIN 715:2011.
Bearings with a spherical locating surface on the housing locating washer correspond to ISO 20516:2007 and DIN 711:2010 as well as DIN 715:2011.
Chamfer dimensions
The limiting dimensions for chamfer dimensions correspond to DIN 620‑6:2004. Overview and limiting values ➤ link. Nominal value of chamfer dimension ➤ link.
Tolerances
The tolerances for the dimensional and running accuracy of axial deep groove ball bearings correspond to tolerance class Normal in accordance with ISO 199:2014. Tolerance values in accordance with ISO 199 ➤ Table to ➤ Table.
Suffixes
For a description of the suffixes used in this chapter ➤ Table and medias interchange http://www.schaeffler.de/std/1B69.
Suffixes and corresponding descriptions
Suffix |
Description of suffix |
|
---|---|---|
MP |
Solid brass cage, ball-guided |
Standard |
P5 |
Bearing in tolerance class 5 |
Special design, |
P6 |
Bearing in tolerance class 6 |
Special design, available by agreement |
Structure of bearing designation
Examples of composition of bearing designation
The designation of bearings follows a set model. Examples ➤ Figure and ➤ Figure. The composition of designations is subject to DIN 623‑1 ➤ Figure.
Axial deep groove ball bearing, single direction, with spherical housing locating washer and support washer: designation structure |
![]() |
Axial deep groove ball bearing, double direction, with spherical housing locating washers: designation structure |
![]() |
Dimensioning
Equivalent dynamic bearing load
P = Fa
Axial deep groove ball bearings can only support axial forces ➤ section. As a result, P = Fa ➤ Equation.
Equivalent dynamic load
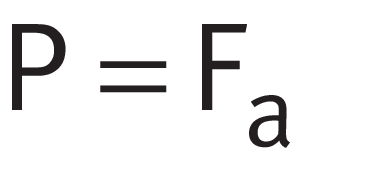
Legend
P | N |
Equivalent dynamic bearing load |
Fa | N |
Axial load |
Equivalent static bearing load
P0 = F0a
Since the bearings can only support axial loads, P0 = F0a ➤ Equation.
Equivalent static load
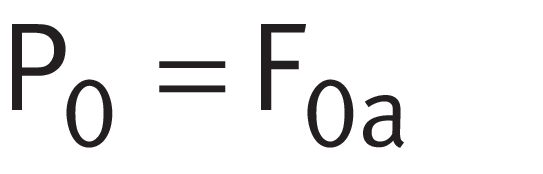
Legend
P0 | N |
Equivalent static bearing load |
F0a | N |
Largest axial load present (maximum load) |
Static load safety factor
S0 = C0/P0
In addition to the basic rating life L (L10h), it is also always necessary to check the static load safety factor S0 ➤ Equation.
Static load safety factor
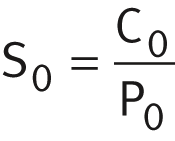
Legend
S0 | - |
Static load safety factor |
C0 | N |
Basic static load rating |
P0 | N |
Equivalent static bearing load |
Minimum load
In order to prevent damage due to slippage, a minimum axial load of Fa min is required
Under axial load, the balls are guided under favourable rolling conditions at the base of the groove. This deteriorates, however, if the centrifugal force occurring at higher speeds and very low loads presses the balls outwards. In this case, detrimental sliding motions can occur between the rolling elements and the raceways due to centrifugal forces and gyroscopic moments. In order to prevent these sliding motions, the bearings must be subjected to the minimum axial load Fa min ➤ Equation. This can also be achieved by means of preloading, for example using springs. The minimum load factor A is given in the product tables. For nmax, the maximum operating speed must be used.
Minimum axial load
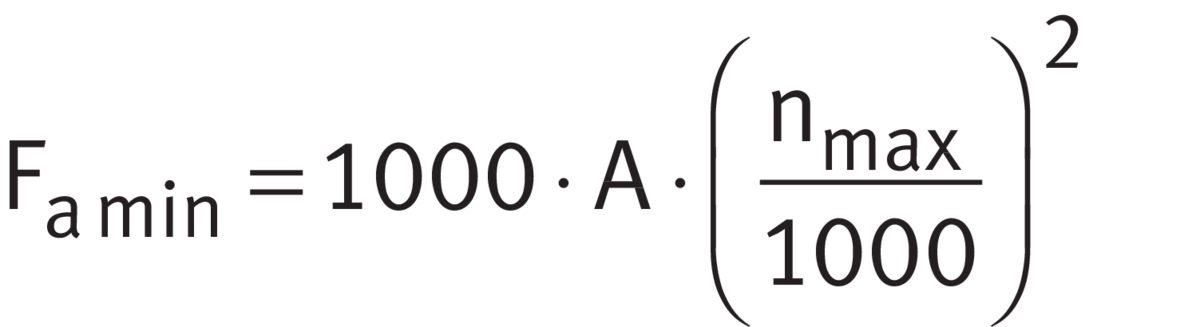
Legend
Fa min | N |
Minimum axial load |
A | - |
Minimum load factor ➤ link |
nmax | min–1 |
Maximum operating speed |
Design of bearing arrangements
In the case of misalignments: use spherical support washers or produce the locating surface in the housing to a spherical design
Bearings with spherical housing locating washers can compensate, in conjunction with a spherical bearing seating surface, misalignments between the locating surface in the housing and on the shaft ➤ section. These bearings can be mounted together with support washers also of a spherical design or directly in the housing. In this case, however, the locating surface in the housing must also be of a spherical design.
Shaft tolerances
Single direction bearings should have the shaft tolerance j6 Ⓔ, while k6 Ⓔ should be selected for double direction bearings.
Tolerances for the housing bore
The tolerance of the locating bore is dependent on the running accuracy to be achieved. For normal running accuracy, it should be in the tolerance class E8 Ⓔ, for high running accuracy, it should be in the tolerance class H6 Ⓔ.
Mounting dimensions for the contact surfaces of bearing rings
The contact surfaces for the washers must be of sufficient height
The shoulders on the adjacent construction (shaft and housing) must be sufficiently high that the shaft and housing locating washers are supported over at least half their height. The abutment shoulders should be rigid, flat and perpendicular to the axis of rotation. Proven mounting dimensions for the radii and diameters of abutment shoulders are given in the product tables ➤ link. These dimensions are limiting dimensions (maximum or minimum dimensions); the actual values should not be higher or lower than specified.
Mounting and dismounting
Do not transpose the shaft and housing locating washer
In the case of single direction bearings, it must be ensured that the shaft and housing locating washer are not exchanged with each other but are mounted in the correct position.
On the shaft locating washer, the bore d is ground and the outside diameter d1 is not ground ➤ Figure. For reliable operation, the shaft locating washer should always abut a shoulder of corresponding dimensions or a support ring securely located on the shaft.
As the bearings are not self-retaining, they are easy to mount
Axial deep groove ball bearings are not self-retaining. As a result, the bearing washers and the ball and cage assembly can be mounted separately from each other ➤ section. This gives simplified mounting of the bearings.
Axial deep groove ball bearing, single direction
|
![]() |
Schaeffler Mounting Handbook
Rolling bearings must be handled with great care
Rolling bearings are well-proven precision machine elements for the design of economical and reliable bearing arrangements, which offer high operational security. In order that these products can function correctly and achieve the envisaged operating life without detrimental effect, they must be handled with care.
The Schaeffler Mounting Handbook MH 1 gives comprehensive information about the correct storage, mounting, dismounting and maintenance of rotary rolling bearings http://www.schaeffler.de/std/1B68. It also provides information which should be observed by the designer, in relation to the mounting, dismounting and maintenance of bearings, in the original design of the bearing position. This book is available from Schaeffler on request.
Legal notice regarding data freshness
The further development of products may also result in technical changes to catalogue products
Of central interest to Schaeffler is the further development and optimisation of its products and the satisfaction of its customers. In order that you, as the customer, can keep yourself optimally informed about the progress that is being made here and with regard to the current technical status of the products, we publish any product changes which differ from the printed version in our electronic product catalogue.
We therefore reserve the right to make changes to the data and illustrations in this catalogue. This catalogue reflects the status at the time of printing. More recent publications released by us (as printed or digital media) will automatically precede this catalogue if they involve the same subject. Therefore, please always use our electronic product catalogue to check whether more up-to-date information or modification notices exist for your desired product.
Further information
In addition to the data in this chapter, the following chapters in Technical principles must also be observed in the design of bearing arrangements: